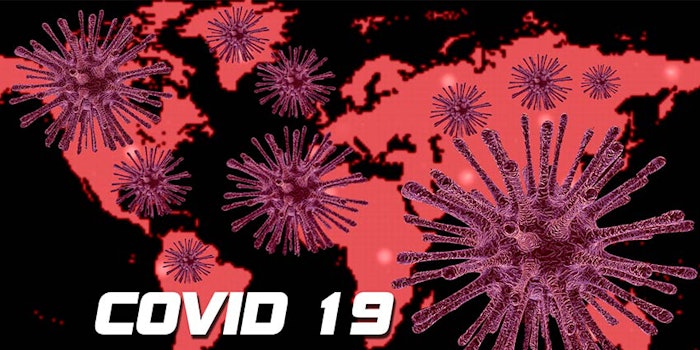
Sabinsa has released its responding measures for keeping its staff and consumers safe during the coronavirus (COVID-19) outbreak.
When the World Health Organization (WHO) declared a Public Health Emergency of International Concern, Sabinsa adopted a multi-tiered approach to deal with the virus starting with establishing preparedness strategies for continuity of operations and clear communication.
Regarding staff:
- While manufacturing standards already adhere to the U.S. FDA, FSMA and other international regulatory bodies as part of cGMP compliance, Sabinsa has reinforced the necessity of effective hand washing practices and good hygiene to all corporate, R&D, warehouse and manufacturing facilities’ staff, worldwide.
- Installation of additional hand washing facilities and implementation of increased sanitation practices are in place as per WHO standards, and the latest release from U.S. FDA, compounding with United States Pharmacopoeia (USP) grade ingredients. The company is well stocked with personal protective equipment and antibacterial products.
- Employees are instructed to stay home if they are ill or show symptoms of cold or flu. Regular health checkups are being conducted on an ongoing basis to identify any infections early on to minimize the potential for virus transmission to others.
- The latest updates about COVID-19 are being shared with employees to keep them well informed.
- Virtual communications are being encouraged to cut down on human-to-human contact internally and externally. Social distancing practices are in force.
To customers:
- Sabinsa expects no significant disruption in client services and remains ready to respond to customer needs via phone, email and where possible by video services. Its manufacturing facilities are operating normally, and at full staff, albeit with heightened health and safety protocols in place.
- The company has fulfilled its commitments to farmers last season to acquire several key herbs that meet Sabinsa’s standards, most of which were processed to its specifications immediately after harvest, leaving ample material on hand. Sabinsa will continue those cultivation and harvesting relationships with the farmers it has worldwide.
- Its advance procurement planning on several other important botanicals, and its probiotic and enzymes, ensures any material required for further processing is always in stock, so the company has at least 6 months and in many cases up to one year of inventory.
- A robust database system is in place to identify critical suppliers and their sourcing locations, especially in heavily impacted areas or those with fewer available support resources.
- Sabinsa is working closely with its vendors and farmers, beyond ensuring continuous supply, to confirm they are following strict hygienic processes throughout.
- Cargo shipments to its global warehouses are currently proceeding uninterrupted, but should that change for any reason, its warehouses across the world are already well stocked with key ingredients, and shipments to customers are occurring normally.
- The company consistently keeps three to four months of finished products stock for supplying customers in all warehouses worldwide. Those locations include three warehouses in the United States (Utah & NJ), two each in Germany, Japan and Australia (Sydney & Melbourne) and one each in Poland, Canada, South Africa, Korea and Dubai. Sabinsa is monitoring the stock in these warehouses continuously, along with keeping them hygienic and sanitary at all times.
To summarize, Sabinsa has not experienced any interruption in its manufacturing and supply chain operations, and foresees no disruptions in its ability to supply ingredients, even with demand increasing as it does in times of crisis.
While the company has taken measures to ensure business as usual, the situation remains fluid. One of the challenges is increased uncertainty.